IChemE Junior Sargent Medal
Feb 17, 2022 — Atlanta, GA

Fani Boukouvala, assistant professor in the School of Chemical and Biomolecular Engineering
Fani Boukouvala, assistant professor in the School of Chemical and Biomolecular Engineering and faculty member of the Renewable Bioproducts Institute, is the first recipient of the Institution of Chemical Engineers' Junior Sargent Medal, which honors an early-career individual who has made a significant recent contribution to research into computer-aided product and process engineering.
The award recognizes Boukouvala's development of novel computational tools for design and optimization of multi-scale, complex systems using both data-driven concepts and traditional chemical engineering fundamentals.
Walter Rich
Blair Brettmann Named 2021 Rising Star by American Chemical Society
Feb 16, 2022 — Atlanta, GA

Blair Brettmann Named 2021 Rising Star by American Chemical Society
Blair Brettmann, assistant professor in the School of Chemical and Biomolecular Engineering (ChBE) and faculty member of the Renewable Bioproducts Institute (RBI) was recognized as a rising star in the February 9, 2022 special issue of ACS Polymers Au journal. The journal is published by the American Chemical Society (ACS), founded in 1876 and chartered by the U.S. Congress. They are one of the world’s largest scientific organizations with membership of over 151,000 in 140 countries.
The editors of ACS Polymers Au invited 13 outstanding early career polymer scientists who have been leading cutting-edge, novel, and impactful research in their independent laboratories to submit peer-reviewed manuscripts for a virtual special issue highlighting the 2021 Rising Stars in Polymers.
Brettmann received her B.S. in chemical engineering from the University of Texas at Austin in 2007 and her Ph.D. in chemical engineering from MIT in 2012 with Bernhardt Trout. Following her Ph.D., Brettmann was a senior research engineer at Saint-Gobain (2012–2014) and a postdoctoral researcher at the Institute for Molecular Engineering at the University of Chicago with Matt Tirrell (2014–2016). Her research focuses on linking molecular to micron-scale phenomena to polymer processing to enable rapid and science-driven formulation and product development. More information about Brettmann and her research can be found here: www.brettmannlab.gatech.edu.
Her article for the special issue is titled “Solvent effects on the elasticity of electrospinnable polymer solutions.” Article DOI: 10.1021/acspolymersau.1c00041.
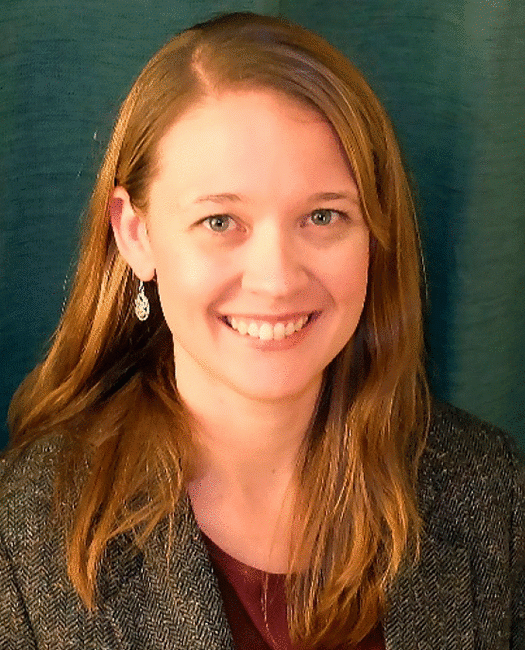
Blair Brettmann, assistant professor in the School of Chemical and Biomolecular Engineering (ChBE) and faculty member of the Renewable Bioproducts Institute
Walter Rich
Agribusiness and Forest Product Innovations Among Projects Emphasized In NIFA Director Tour of Georgia Tech
Feb 15, 2022 — Atlanta, GA

In January, Georgia Tech hosted Carrie Castille, director of the National Institute of Food and Agriculture (NIFA), on campus to show Georgia Tech’s impact on food processing, agricultural, and forestry research.
NIFA, which operates within the U.S. Department of Agriculture, was created in 2008 to further enhance the nation’s agricultural research and education. The agency works to address the agricultural issues affecting people’s daily lives and the nation’s future by partnering with other federal agencies, universities, and nonprofits. NIFA funds research and educational initiatives in order ensure the long-term viability of agriculture in the United States.
Agriculture and forestry are serious business here in the state of Georgia. According to the University of Georgia’s Center for Agribusiness and Economic Development, Georgia’s forest industry accounts for a total economic contribution to the state of $17.7 billion and supports more than 73,300 jobs in Georgia. Agriculture contributes approximately $73.3 billion annually to Georgia's economy and ranks No. 1 in the U.S. for broilers, hatching eggs, and peanuts. One in seven Georgians works in agriculture, forestry, or related fields. While Georgia Tech is not a land-grant university, Georgia Tech researchers work alongside university partners across the state, merging engineering and technology expertise with partners in traditional agricultural sciences.
Castille and her staff met with researchers at Georgia Tech’s Renewable Bioproducts Institute (RBI) along with GTRI’s Agricultural Technology Research Program (ATRP). RBI creates a competitive edge and insight into the future of forest products. Their professional scientists and engineers work together to provide information and offer solutions required by a rapidly changing market. GTRI’s ATRP is a state-funded research program meant to help Georgia’s agriculture economy and poultry industry. ATRP drives transformational innovation, developing new methods and systems specifically designed for poultry, agribusiness, and food manufacturing applications. These innovations are created to maximize productivity and efficiency, advance safety and health, and minimize environmental impacts. Their goal is to transition technologies from concept to commercialization, as quickly and economically as possible.
Blair Meeks
wmeeks7@gatech.edu
Assistant Vice President External Communications
Researchers Discover Crystalline Zeolites in a Nanotubular Shape
Jan 27, 2022 — Atlanta, GA

Zeolites, which are crystalline porous materials, are very widely used in the production of chemicals, fuels, materials, and other products.
Zeolites, which are crystalline porous materials, are very widely used in the production of chemicals, fuels, materials, and other products. So far, zeolites have been made as 3D or 2D materials. This has changed with the recent discovery of crystalline zeolites in a nanotubular (1D) shape, by researchers at the Georgia Institute of Technology, Stockholm University, and Penn State University. The findings were published in the Jan. 6 issue of Science.
"A discovery like this is one of the most exciting parts of our research," said Sankar Nair, principal investigator and professor in the School of Chemical & Biomolecular Engineering at Georgia Tech. "We're increasingly used to doing research that has a pre-determined application at the end of it, so this is a reminder that fundamental discoveries in materials science are also exciting and important."
Zeolites have pores roughly the size of many types of molecules, and scientists and engineers have used the varied sizes, shapes, and connections of the pores to discriminate between molecules of different sizes, allowing for the production of chemicals suitable for plastic production, or for the separation of undesired molecules from desired ones, as examples.
The team was designing syntheses to assemble 2D zeolite materials. In an unexpected turn of events, some of the results indicated that a new type of assembly process was occurring. Indeed, one such case led to a novel 1D zeolite material that had a tube-like structure with perforated porous walls. This 1D material, termed a zeolitic nanotube, was unlike any zeolite ever synthesized or discovered in nature previously.
"Zeolite nanotubes could be used to make entirely new types of nanoscale components that can control transport of mass or heat or charge, not only down the length of the tube the pipe, but also in and out through the perforated walls," said Nair.
Resolving the detailed arrangement of the atoms in the zeolite nanotube was a challenging task, for which the Georgia Tech researchers teamed up with zeolite crystallography experts at Stockholm University and Penn State. They found that the nanotube walls had a unique arrangement of atoms that are not known in 3D or 2D zeolites. This same arrangement is also responsible for forcing the zeolite to form as a 1D tube rather than a 2D or 3D material.
"This is the first example of a new class of nanotubes, and its unique and well-defined structure provides exciting ideas and opportunities to design zeolite nanomaterials," said Tom Willhammar, co-investigator and researcher at Stockholm University. "Through further work, we hope that different zeolitic nanotubes could be obtained with variations in pore size, shape and chemistry."
Put plainly—a nanometer-scale tube made from a 1D material with regular, perforated holes on the sides is now available for exploration. In addition to this being a fundamental scientific discovery that could change the way we think about designing porous materials, the researchers see potential for many practical applications.
"The unique structural attributes of these materials will allow for an array of potential applications in membrane separations, catalysis, sensing, and in energy devices where mass or energy transport are crucial," said Christopher W. Jones, co-principal investigator and professor at Georgia Tech. "The materials may have unique mechanical properties, as well, finding applications in composite materials, as carbon nanotubes have done. At this stage, the sky is the limit, and we hope researchers will look for creative ways to deploy these materials for the benefit of humanity."
Walter Rich
Researchers Using $5.3 Million in DoE Funding to Reduce Energy, Water Consumption, and Emissions in Fiber Composite Products and Wallboard Manufacturing
Jan 25, 2022 — Atlanta, GA

Cyrus Aiden, Devesh Ranjan, and Srinivas Garimella
Two teams of researchers from the George W. Woodruff School of Mechanical Engineering have received Department of Energy funding to work with corporate partners to reduce the energy consumption and carbon emissions of energy intensive manufacturing processes.
Principal investigator Professor Cyrus Aidun, along with Eugene C. Gwaltney Jr Chair Devesh Ranjan, have received $3 million dollars in funding from the DoE for their work on advanced multiphase (MP) forming for enhanced efficiency of drying paper, tissue, board, nonwovens and other fiber composite products. The research is being conducted with Sandia National Lab and industry partners Kimberly-Clark and Solenis. In response to receiving the award, Professor Aidun said, "I am pleased that Department of Energy has recognized our research in multiphase forming to be a transformative technology that significantly reduces the need for fossil fuel energy and water consumption in a major manufacturing industry."
This industry is the third largest consumer of energy within the United States. The research team headed by Aidun is working to provide energy savings to the industry by bringing MP forming to large-scale commercial applications. The process of MP forming involves replacing a traditionally water-based carrier fluid with high-density (HD) foam within the manufacturing process of fiber-based materials. The reduction in water allows for an additional 30% reduction in the demand of evaporative drying, resulting in less energy consumption. In comparison to traditional methods of manufacturing, MP forming results in a 25% decrease in CO2 emissions. When fully integrated into a dedicated facility, the decrease in CO2 emissions could potentially reach 50%.
A large focus of Aidun’s research is on overcoming the barriers that are currently preventing MP forming from being used in commercial applications. Many of the complications stem from HD foam containing significantly different flow characteristics than water. Additional research into its behavior and how to manage it within commercial implementations is required. The focus of that research will be on achieving a deeper understanding of how fibers are suspended within HD foam and how to consistently orient the fibers for creating certain products.
Srinivas Garimella, the Hightower Chair in Engineering and Director of the Sustainable Thermal Systems Laboratory in the Woodruff School, received a $2.3 million grant from the Department of Energy for research on “Advanced Techniques for Energy Input Reduction in Gypsum Wallboard Drying.”
Garimella and the Georgia Tech Research Corporation are working with the largest wallboard manufacturer in the world, Saint-Gobain, to reduce energy, water consumption, and carbon emissions in the manufacture of gypsum board. Gypsum wallboard manufacturing is a $22.5 billion dollar industry, which involves significant energy use and carbon dioxide emissions, consuming 445 kWh of energy per ton of product while producing 80 kg/ton of CO2 emissions. According to Garimella, “This project has significant potential to disrupt an energy-intensive industry and can lead to energy savings of more than 2.1 × 107 GJ annually.” The partnership between Garimella and Saint- Goblin is committed to reimagining the manufacturing process and reduce the industry’s carbon footprint.
In this three-year collaboration, the team will develop and implement microwave-based calcination and particle size optimization for the slurry to achieve the goals of reducing water and energy consumption in the production of gypsum wallboard. With the funding from this award, Garimella and his team have the potential to increase efficiency and hit their goal of a 50% reduction in energy consumption and CO2 emissions in the manufacture of gypsum wallboard.
Combined, the two projects have the potential to reshape resource intensive manufacturing processes and reduce the environmental impact of paper, tissue, board, nonwovens and gypsum board production in Georgia and around the world.
FUNDING: These projects are being funded by the Advanced Manufacturing Office of the DOE Office of Energy Efficiency and Renewable Energy, award numbers DE-EE0009394 and DE-EE0009396.
Walter Rich
Producing Active Pharmaceutical Ingredients from Lignin using Green Chemistry
Jan 11, 2022 — Atlanta, GA

Green Chemistry Journal (Header). Pictured: wood pulp is a major source for lignin.
Lignin, which is second to cellulose as the most abundant organic material on Earth, could be a source for the production of active pharmaceutical ingredients (APIs) using Green Chemistry production processes that reduce waste. APIs are the central part of any drug that produce the intended beneficial effect. (Other parts of the drug, called the excipient, aid in the delivery of the API medication to the targeted area of the human body).
Lignin, an abundant renewable material, can be converted to phenol and catechol, which can then be further converted into four important APIs: paracetamol (Tylenol®), acetyl salicylic acid (Aspirin®), amoxicillin (as sole API or as combination with potassium clavulanate (Augmentin®), and epinephrine (adrenaline, known also as trademark Adrenaline®).
A perspective paper by a team of Georgia Tech researchers focused on these important ingredients examines API production from renewable materials, in this case Lignin as the renewable material, and how Green Chemistry production could combine a low environmental footprint with high quality and economical manufacture of pharmaceuticals using Lignin.
Their paper, “Production of active pharmaceutical ingredients (APIs) from lignin-derived phenol and catechol,” was published in the October 7, 2021 issue of Green Chemistry.
The research team that wrote the paper include: Andreas Bommarius, professor of Chemical and Biomolecular Engineering at the Georgia Institute of Technology; Carsten Sievers, associate professor in the School of Chemical and Biomolecular Engineering at the Georgia Institute of Technology; Jimin Park, a Ph.D. student in the Georgia Tech School of Chemical and Biomolecular Engineering; Jason Kang, Siddarth Seemakurti, and Jasmine Ramirez, who are each pursuing a Bachelor of Science in the Georgia Tech School of Chemical and Biomolecular Engineering; Marta Hatzell, an associate professor in the Woodruff School of Mechanical Engineering at the Georgia Institute of Technology; and Megan Kelly, a graduate student at the University of Wisconsin. Park, Sievers, and Bommarius are affiliated with Georgia Tech’s Renewable Bioproducts Institute.
APIs are traditionally created by pharmaceutical companies and most of this production has shifted oversees where costs of production are lower than the USA and Europe. (As a result, rigorous guidelines and inspections have been put into place when these API ingredients are imported).
API production often suffers from unfavorable Green Chemistry metrics. Green Chemistry is a new way of thinking about how chemistry and chemical engineering (i.e. processes) are done. Benefits of applying Green Chemistry can include conserving energy, producing less hazardous substances, creating more sustainable processes, producing less waste, producing less pollution, using renewable feedstocks, designing systems holistically using life cycle thinking, etc.
With current supply chain disruptions, there has been renewed interest in reshoring drug production. New initiatives, such as the Food and Drug Administration’s (FDA) Emerging Technology Program, have tried to reduce barriers to advanced manufacturing techniques that can make domestic production more economically attractive. A collaboration between the FDA and the Biomedical Advanced Research and Development Authority (BARDA) is trying to develop mobile manufacturing platforms to produce APIs on demand near point of care. Furthermore, the European Commission has been proposing road maps to reduce dependence on outsourced products and secure Europe's supply chain.
Lignin, the second most prevalent component of plant biomass after cellulose, fills several criteria for a desirable fossil resource substitute through its abundance, renewability, and carbon neutrality. However, it is difficult to convert because it naturally occurs in a heterogeneous composite of cellulose, hemicellulose, and lignin from which it must first be liberated. In addition, lignin itself is complex, irregular, and highly oxygenated, and its purpose of providing rigidity in the plant cell wall contributes to its resistance to biomass conversion.
Despite these difficulties, much progress has been made on overcoming them through a focus on the fractionation of lignocellulose, depolymerization of lignin, and upgrading the resulting monomers into valuable products.
Walter Rich
Fall 2021 IEN Seed Grant Winners Announced
Dec 07, 2021 — Atlanta, GA

IEN Seed Grant Icon 2021
The Institute for Electronics and Nanotechnology at Georgia Tech has announced the winners for the 2021 Fall Facility Seed Grants. The primary purpose of this program is to give first- or second-year graduate students in diverse disciplines working on original and un-funded research in micro- and nano-scale projects the opportunity to access the most advanced academic cleanroom space in the Southeast. In addition to accessing the high-level fabrication, lithography, and characterization tools in the labs, the awardees will have the opportunity to gain proficiency in cleanroom and tool methodology and access the consultation services provided by research staff members of the IEN. Seed Grant awardees are also provided travel support to present their research at a scientific conference.
In addition to student research skill development, this bi-annual grant program gives faculty with novel research topics the ability to develop preliminary data to pursue follow-up funding sources. The Facility Seed Grant program is supported by the Southeastern Nanotechnology Infrastructure Corridor (SENIC), a member of the National Science Foundation’s National Nanotechnology Coordinated Infrastructure (NNCI).
Since the start of the grant program in 2014, seventy-two projects from ten different schools in Georgia Tech’s Colleges of Engineering and Science, as well as the Georgia Tech Research Institute and 3 other universities, have been seeded.
The 4 winning projects in this round were awarded IEN cleanroom and lab access time to be used over the next year. In keeping with the interdisciplinary mission of IEN, the projects that will be enabled by the grants include research in semiconductor technology, opto-electronic materials and designs, quantum computing, and polymer nanostructures.
The Fall 2021 IEN Facility Seed Grant Award winners are:
In-situ Electron Microscopy Biasing Experiments on Ferroelectric Oxides on Ge Substrates
PI: Asif Khan and Joshua Kacher | Student: Nashrah Afroze
School of Electrical and Computer Engineering/School of Materials Science and Engineering
Fabrication of Dielectric Resonant Optical Metamaterials using 3D Printed Patterns
PI: Sourabh Saha | Student: Vidhukiran Venkataraman
George W. Woodruff School of Mechanical Engineering
Realization of Microscale Mechanical Bistable Junction
PI: Chengzhi Shi | Student: Chenzhe Wang
George W. Woodruff School of Mechanical Engineering
Fabrication and Characterization of Surface-Modified Polymers
PI: Akanksha Menon | Student: Walter Parker
George W. Woodruff School of Mechanical Engineering
The Southeastern Nanotechnology Infrastructure Corridor (SENIC), a member of the National Nanotechnology Coordinated Infrastructure (NNCI), is funded by NSF Grant ECCS-2025462.
Related Links
Christa M. Ernst - Interdisciplinary Research Communications Program Manager
Topics: Materials | Nanotechnology | Robotics
Georgia Institute of Technology| christa.ernst@research.gatech.edu
Making Martian Rocket BioFuel on Mars
Oct 25, 2021 — Atlanta, GA

Artist's conception of astronauts and human habitats on Mars. Courtesy: NASA
Researchers at the Georgia Institute of Technology have developed a concept that would make Martian rocket fuel, on Mars, that could be used to launch future astronauts back to Earth.
The bioproduction process would use three resources native to the red planet: carbon dioxide, sunlight, and frozen water. It would also include transporting two microbes to Mars. The first would be cyanobacteria (algae), which would take CO2 from the Martian atmosphere and use sunlight to create sugars. An engineered E. coli, which would be shipped from Earth, would convert those sugars into a Mars-specific propellant for rockets and other propulsion devices. The Martian propellant, which is called 2,3-butanediol, is currently in existence, can be created by E. coli, and, on Earth, is used to make polymers for production of rubber.
The process is outlined in a paper, “Designing the bioproduction of Martian rocket propellant via a biotechnology-enabled in situ resource utilization strategy,” published in the journal Nature Communications.
Rocket engines departing Mars are currently planned to be fueled by methane and liquid oxygen (LOX). Neither exist on the red planet, which means they would need to be transported from Earth to power a return spacecraft into Martian orbit. That transportation is expensive: ferrying the needed 30 tons of methane and LOX is estimated to cost around $8 billion. To reduce this cost, NASA has proposed using chemical catalysis to convert Martian carbon dioxide into LOX, though this still requires methane to be transported from Earth.
As an alternative, Georgia Tech researchers propose a biotechnology based in situ resource utilization (bio-ISRU) strategy that can produce both the propellant and LOX from CO2. The researchers say making the propellant on Mars using Martian resources could help reduce mission cost. Additionally, the bio-ISRU process generates 44 tons of excess clean oxygen that could be set aside to use for other purposes, such as supporting human colonization.
“Carbon dioxide is one of the only resources available on Mars. Knowing that biology is especially good at converting CO2 into useful products makes it a good fit for creating rocket fuel,” said Nick Kruyer, first author of the study and a recent Ph.D. recipient from Georgia Tech’s School of Chemical and Biomolecular Engineering (ChBE).
The paper outlines the process, which begins by ferrying plastic materials to Mars that would be assembled into photobioreactors occupying the size of four football fields. Cyanobacteria would grow in the reactors via photosynthesis (which requires carbon dioxide). Enzymes in a separate reactor would break down the cyanobacteria into sugars, which could be fed to the E. coli to produce the rocket propellant. The propellant would be separated from the E. coli fermentation broth using advanced separation methods.
The team’s research finds that the bio-ISRU strategy uses 32% less power (but weighs three times more) than the proposed chemically enabled strategy of shipping methane from Earth and producing oxygen via chemical catalysis.
Because the gravity on Mars is only a one-third of what is felt on Earth, the researchers were able to be creative as they thought of potential fuels.
“You need a lot less energy for lift-off on Mars, which gave us the flexibility to consider different chemicals that aren’t designed for rocket launch on Earth,” said Pamela Peralta-Yahya, a corresponding author of the study and an associate professor in the School of Chemistry & Biochemistry and ChBE who engineers microbes for the production of chemicals. “We started to consider ways to take advantage of the planet’s lower gravity and lack of oxygen to create solutions that aren’t relevant for Earth launches.”
“2,3-butanediol has been around for a long time, but we never thought about using it as a propellant. After analysis and preliminary experimental study, we realized that it is actually a good candidate,” said Wenting Sun, associate professor in the Daniel Guggenheim School of Aerospace Engineering, who works on fuels.
The Georgia Tech team spans campus. Chemists, chemical, mechanical, and aerospace engineers came together to develop the idea and process to create a viable Martian fuel. In addition to Kruyer, Peralta-Yahya, and Sun, the group included Caroline Genzale, a combustion expert and associate professor in the George W. Woodruff School of Mechanical Engineering, and Matthew Realff, professor and David Wang Sr. Fellow in ChBE, who is an expert in process synthesis and design.
The team is now looking to perform the biological and materials optimization identified to reduce the weight of the bio-ISRU process and make it lighter than the proposed chemical process. For example, improving the speed at which cyanobacteria grows on Mars will reduce the size of the photobioreactor, significantly lowering the payload required to transport the equipment from Earth.
“We also need to perform experiments to demonstrate that cyanobacteria can be grown in Martian conditions,” said Realff, who works on algae-based process analysis. “We need to consider the difference in the solar spectrum on Mars both due to the distance from the Sun and lack of atmospheric filtering of the sunlight. High ultraviolet levels could damage the cyanobacteria.”
The Georgia Tech team emphasizes that acknowledging the differences between the two planets is pivotal to developing efficient technologies for the ISRU production of fuel, food, and chemicals on Mars. It’s why they’re addressing the biological and materials challenges in the study in an effort to contribute to goal of future human presence beyond Earth.
“The Peralta-Yahya lab excels at finding new and exciting applications for synthetic biology and biotechnology, tackling exciting problems in sustainability,” added Kruyer. “Application of biotechnology on Mars is a perfect way to make use of limited available resources with minimal starting materials.”
The research was supported by a NASA Innovative Advanced Concepts (NIAC) Award.
Citation: Kruyer, et al. “Designing the bioproduction of Martian rocket propellant via a biotechnology-enabled in situ resource utilization strategy” Nature Communications. 10.1038/s41467-021-26393-7.
About Georgia Tech
The Georgia Institute of Technology, or Georgia Tech, is a top 10 public research university developing leaders who advance technology and improve the human condition. The Institute offers business, computing, design, engineering, liberal arts, and sciences degrees. Its nearly 40,000 students, representing 50 states and 149 countries, study at the main campus in Atlanta, at campuses in France and China, and through distance and online learning. As a leading technological university, Georgia Tech is an engine of economic development for Georgia, the Southeast, and the nation, conducting more than $1 billion in research annually for government, industry, and society.
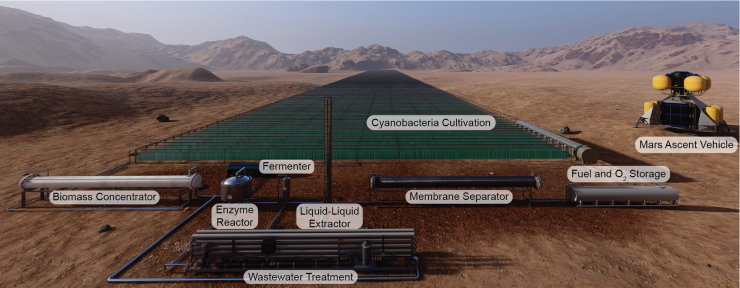
Photobioreactors the size of four football fields, covered with cyanobacteria, could produce rocket fuel on Mars. Courtesy: BOKO mobile study
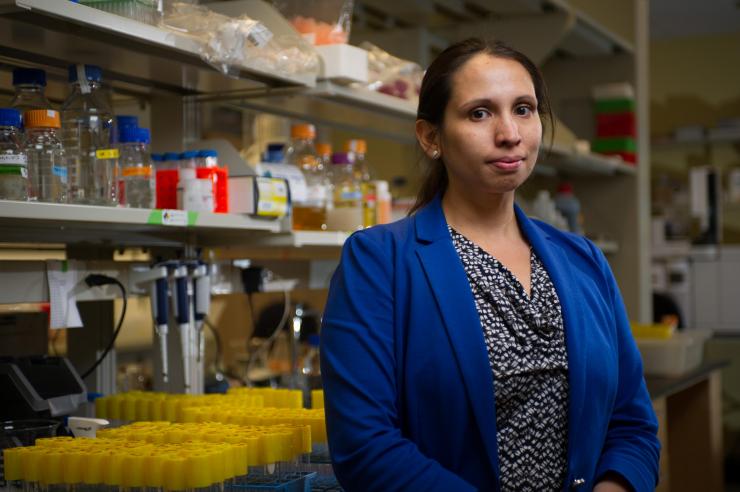
Pamela Peralta-Yahya, Schools of Chemistry & Biochemistry and Chemical and Biomolecular Engineering
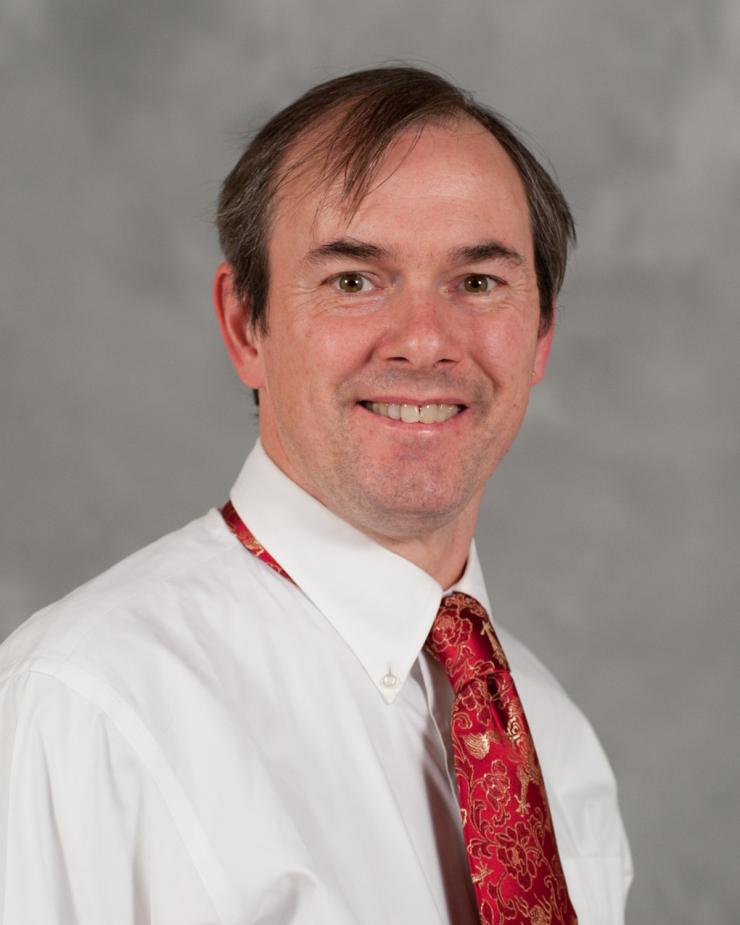
Matthew Realff, School of Chemical and Biomolecular Engineering
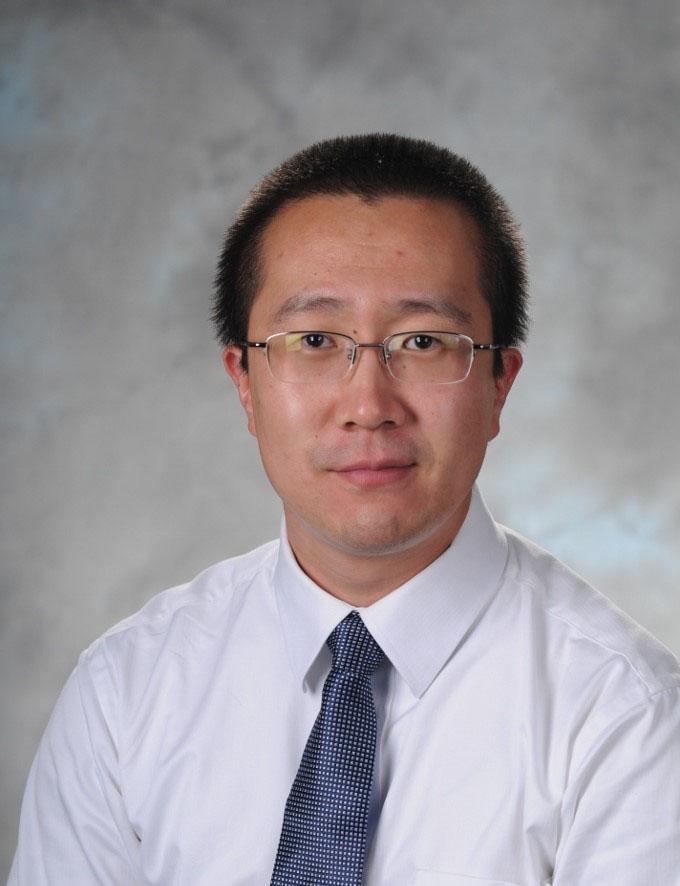
Wenting Sun, Daniel Guggenheim School of Aerospace Engineering
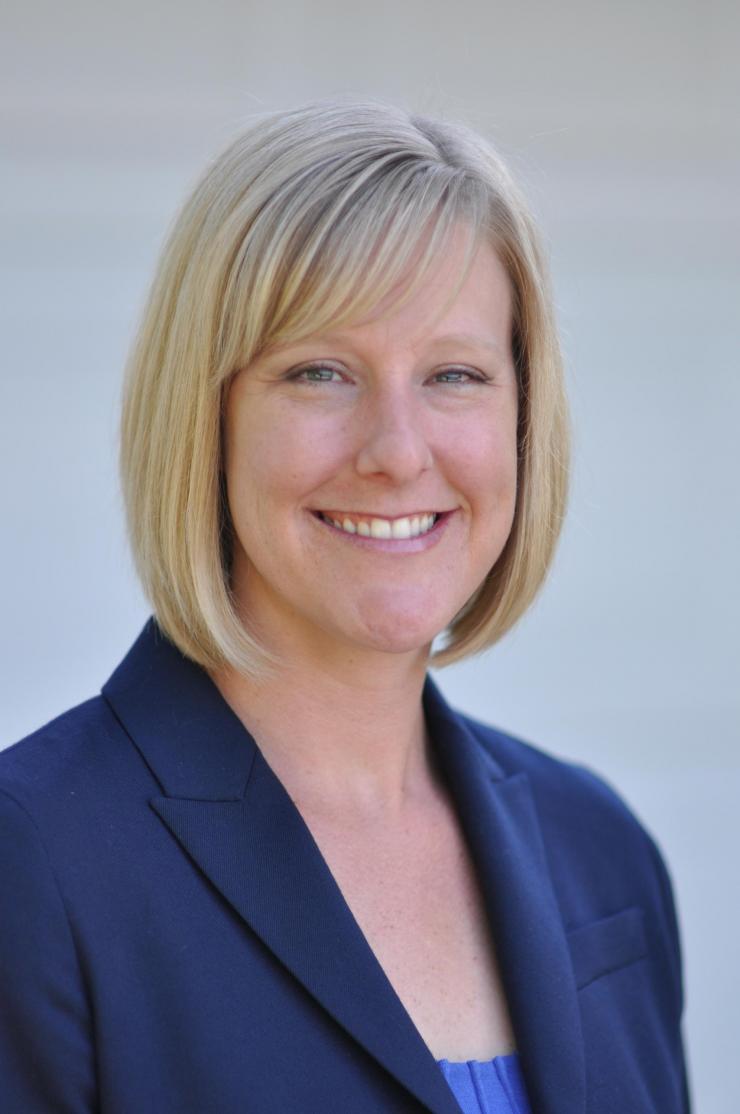
Caroline Genzale, George W. Woodruff School of Mechanical Engineering
Jason Maderer
College of Engineering
maderer@gatech.edu
Museum Opening Update
Sep 09, 2021 — Atlanta, GA

Depiction of Robert C. Williams Museum of Papermaking main gallery
The Robert C. Williams Museum of Papermaking has reopened after summer construction in the Renewable Bioproducts Institute.
The Museum is open Monday-Friday, 9-5, and is free to visit. Groups of 10 or more must book a fee-based program in advance.
Wild/Life, a juried exhibit organized by the Guild of Book Workers, will open on Friday, September 17, 2021.
Virginia Howell
Museum Director
404-894-5726
Efficiency Leap in Separating Para-xylene Using New Carbon Membranes
Sep 08, 2021 — Atlanta, GA

Georgia Tech used these carbon membrane materials to separate para-xylene from o-xylene. (Photo credit: Christopher Moore, Georgia Tech)
The petrol industry recognizes the importance of para-xylene, given its many uses in everyday products, from plastic soda bottles to polyester fiber.
The challenge is that xylenes travel in threes and are virtually identical, making it extremely difficult to efficiently separate and purify para-xylene from its less used siblings such as ortho-xylene. These molecules’ size differs by one-tenth of a nanometer. However, membranes with tiny pores engineered to differentiate these molecules can potentially enable this important separation.
Building on long-term research with ExxonMobil, researchers at the Georgia Institute of Technology have uncovered new insights into the fabrication of carbon membranes that have the potential to drive significant cost savings once the solution for xylene isolation separation is scaled for industrial use.
The findings were reported in the September 6, 2021 issue of the Proceedings of the National Academy of Sciences.
The work focuses on “carbon-based molecular sieves,” made by heating thin layers of materials in such a way as to drive off all the atoms other than carbon, resulting in a charcoal-like substance that has molecule-sized holes. In 2016 researchers at Georgia Tech and Exxon Mobil first demonstrated that a new carbon-based molecular sieve membrane could successfully separate xylene molecules and extract the super-useful para-xylene from the pack.
Now, Georgia Tech has advanced this work, devising improved carbon barriers that allows the skinnier p-xylene to slip through more rapidly, while rejecting the wider molecules. Importantly, the team discovered a powerful relationship between the bonding chemistry of the carbons and the mobility of xylenes through the carbon membranes.
The performance of the carbon membranes — if realized at industrial scales — could significantly lower energy costs compared with refining processes such as the standard crystallization method or adsorption-based method. The former approach involves freezing the xylene molecules in which only the para-xylene forms crystals, making it easy to isolate, but requiring substantial energy investment. The latter approach reduces energy consumption compared to crystallization but requires expensive and complex equipment to operate. The issue with membranes, according to Georgia Tech researchers, is the approach has only worked well in the lab environment, not in an industrial setting.
“We have made more stable materials by changing the polymer precursor we use. Then by changing how we transform the polymer into the carbon, we’ve made the membranes more productive,” said Ryan Lively, an associate professor in Georgia Tech’s School of Chemical & Biomolecular Engineering and the paper’s corresponding author.
Just how much more productive? The team has shown the new materials can lead to purification systems that are estimated to be “three to six times lower cost than other state-of-the-art methods,” Lively said.
Lively estimates that separation and purification account for around half the energy consumed in producing commodity chemicals and fuels. Globally, the amount of energy used in conventional separation processes for aromatics, for example, benzene toluene, is equal to that produced by about 20 average-sized power plants.
This advancement could have a big impact on petrol chemical energy consumption. The research was funded by ExxonMobil and builds on more than 15 years of collaborative research effort between Georgia Tech and the global oil and gas leader.
“Through collaboration with strong academic institutions like Georgia Tech, we are constantly exploring new, more efficient ways to produce the energy, chemicals, and other products consumers around the world rely on every day," said Vijay Swarup, vice president of research and development at ExxonMobil Research and Engineering Company.
The Georgia Tech researchers also uncovered new insights regarding the carbon structure itself. The team observed that subtle changes in the ratio of three dimensional to two-dimensional carbon centers in the membrane led to impressively large changes in the mobility of xylene isotherms within that material. They observed that a change in this ratio (the sp3/sp2 carbon ratio) from 0.2 to 0.7 led to a factor of 1000 increase in the productivity of the membrane. Surprisingly, the membrane largely maintained its selectivity, or its ability to do the xylene isomer separation, despite these changes in carbon structure.
“The more three-dimensional carbons are in there, the higher the productivity,” said M.G. Finn, professor and chair of Georgia Tech’s School of Chemistry and Biochemistry and co-corresponding author on the article. “The more you crank up productivity, while maintaining the same selectivity, the less membrane you need to handle the same amount of xylene feed. From a design perspective, it shows that you have this enormous control over how the membrane works by making very small changes in the carbon chemistry,” Finn concluded.
ExxonMobil Research & Engineering funded this research.
Citation: Yao Ma, Nicholas C. Bruno, Fengyi Zhang, M. G. Finn, and Ryan P. Lively. “Zeolite-like performance for xylene isomer purification using polymer-derived carbon membranes.” PNAS (Proceedings of the National Academy of Sciences of the United States of America). https://doi.org/10.1073/pnas.2022202118
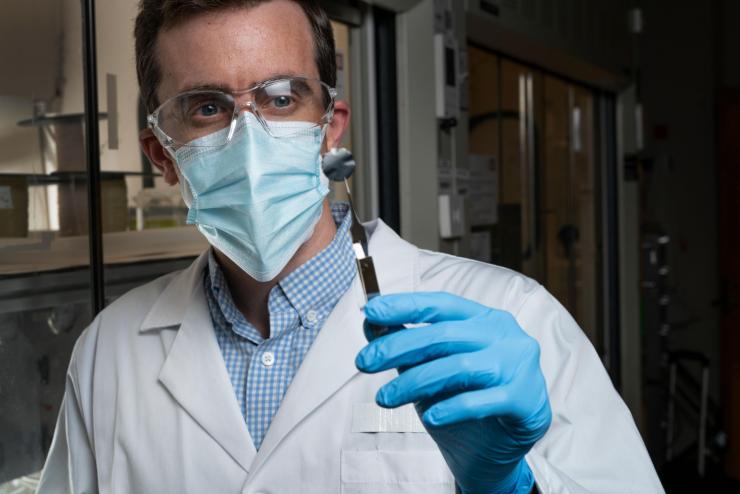
Georgia Tech Associate Professor Ryan Lively holding a small sample used to experimentally understand how the xylenes transport through the carbon structure. (Photo credit: Christopher Moore, Georgia Tech)
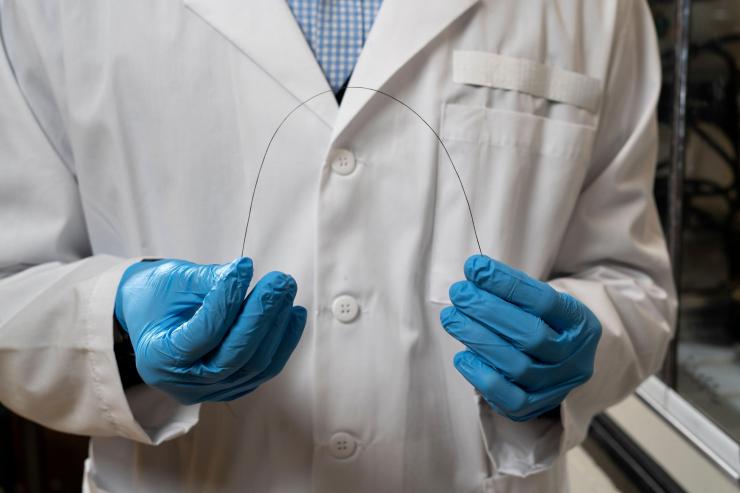
Carbon membranes can be scaled up into carbon fibers, which is the commercial form factor for the membrane system. (Photo credit: Christopher Moore, Georgia Tech)
Anne Wainscott-Sargent