New “Micro-rocker” Bots Are Powered by a Single Electromagnetic Coil
Apr 14, 2022 — Atlanta, GA

Ansari and her team of Georgia Tech researchers have developed microscopic “rocker” robots powered by a single electromagnetic coil that could eventually be injected in living organisms to deliver drugs or repair injuries.
Georgia Tech researchers have shown that robots about the size of a particle of dust are capable of precise bidirectional control. By harnessing the power of a magnetic field generated by only a single electromagnetic coil, the mobile micro-robots are the smallest of their type.
“There are swimmer micro-robots that move in a fluid with similar size, but these are the smallest ‘walking’ robots that move on a solid surface,” said Azadeh Ansari, the Sutterfield Family Early Career Assistant Professor at Georgia Tech School of Electrical and Computer Engineering (ECE).
The Georgia Tech study was recently published in the Journal of Micro-Bio Robotics. Currently, most magnetically-actuated micro-bot systems rely on adding multiple electromagnets to enable full control, resulting in higher power consumption and less flexible setups. Being able to demonstrate that a single coil setup is enough for precise bidirectional motion control is a significant hurdle to clear, according to Ansari. With the micro-bots now much easier to operate, the team has been able to demonstrate micromanipulation capabilities.
“With what we’ve shown, we can already think of applying the micro-bots in a lab setting,” said Ansari. “You could have hundreds of robots on the same substrate working akin to ants in a colony.”
In Spring 2019, Ansari’s team showcased larger (two millimeters long) “micro-bristle-bots” that could move by harnessing vibrations. Vibrations are no longer needed to move the micro-bots because of their updated “rocker” design — hence micro-rocker bots. The new design allows the bots to move by performing a stick–slip motion with an out-of-plane magnetic field.
Stick-slip motion basically refers to the two states of the robot; one when the robot is in a pinned/stationary position on the surface and the other when the robot “slips” slightly in one direction and achieves net motion, according to Ph.D. student Tony Wang. When the magnetic field is turned on, the robot will essentially rise and then fall. This motion enables enough kinetic energy to allow the robot to move.
More Than a New Design
Equally as important as the rocker design, the paper demonstrates the novel use of a waveform offset for biasing the direction of the robot's trajectory. The sign of the magnetic field offset (positive or negative), as well as the rocker’s angle with the surface, is what determines the direction the micro-bots will travel. Combined, the rocker design and the magnetic offset make the micro-bots capable of well-controlled, and importantly selectable, movement. The acceleration and deceleration of the micro-rocker bots can further be controlled by changing the frequency of the magnetic field.
The 100-micrometre long micro-bots were 3D printed on to a glass substrate via two-photon lithography and subsequently deposited with a nickel thin film, which acts as a semi-hard magnet in response to external magnetic fields. For many lab applications the robots can be directly printed on the substrate that will go under the microscope, but they can also be printed and transported with a micropipette.
“There are lot of areas the micro-robots can be applied to within the current 2D, under-the-microscope process we’ve established so far,” said Ansari. “But there’s also a future where they can be injected into living organisms to deliver drugs or repair injuries.”
The team is currently working to equip a micro-bot with a tip that could potentially insert nanoparticles into biological tissue for drug delivery or DNA extraction. Their findings will be presented at the Hilton Head Workshop 2022: A Solid-State Sensors, Actuators and Microsystems Workshop this June.
****
Citation: Tony Wang, DeaGyu Kim, Yifan Shi, and Zhijian Hao, Azadeh Ansari “Bidirectional microscale rocker robots controlled via neutral position offset” (Journal of Micro-Bio Robotics, 2022). https://doi.org/10.1007/s12213-022-00149-y
Funding: This work is supported by Georgia Tech Institute for Electronics and Nanotechnology (IEN) and the National Science Foundation Graduate Research Fellowship under Grant No. DGE-1650044. The device fabrication was performed at the Georgia Tech Institute for Electronics and Nanotechnology clean room facilities, a member of the National Nanotechnology Coordinated Infrastructure (NNCI), which is supported by the National Science Foundation (Grant ECCS-1542174).
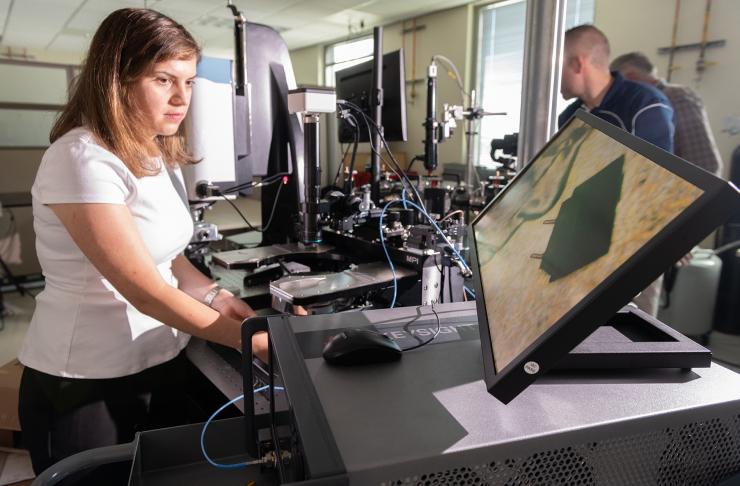
The micro-rocker bots created at Georgia Tech are designed to move by performing a stick–slip motion with an out-of-plane magnetic field. The stick-slip motion makes the robots look like they are walking or wobbling to their destination. The scale of the video is 500 micrometers (half a millimeter), and the red line shows the micro-bots trajectory.
Dan Watson
dwatson@ece.gatech.edu