New Projects Create a Foundation for Next-Gen Flexible Electronics
Mar 16, 2017 — Atlanta, GA

A Georgia Tech researcher displays the flexibility of a new class of electronics. (Credit: Rob Felt)
Four projects set to move forward at the Georgia Institute of Technology aim to lay the groundwork for manufacturing next-generation flexible electronics, which have the potential to make an impact on industries ranging from health care to defense.
The projects, which will take place over the next two years and have a budget of more than $9 million, are backed by NextFlex, the Flexible Hybrid Electronics Manufacturing Innovation Institute, a group of private companies, universities, several state and local governments and not-for-profit organizations with a mission to advance flexible electronics manufacturing in the United States.
Researchers at Georgia Tech are partnering with Boeing, Hewlett Packard Enterprises, General Electric, and DuPont as well other research institutions such as Binghamton University and Stanford University on the projects.
Flexible electronics are circuits and systems that can be bent, folded, stretched or conformed without losing their functionality. The systems are often created using machines that can print components such as logic, memory, sensors, batteries, antennas, and various passives using conductive ink on flexible surfaces. Combined with low-cost manufacturing processes, flexible hybrid electronics unlock new product possibilities for a wide range of electronics used in the health care, consumer products, automotive, aerospace, energy and defense sectors.
Suresh Sitaraman, a professor in the George W. Woodruff School of Mechanical Engineering, who is leading Georgia Tech’s flexible electronics activities, said the technologies have the potential to positively impact some of society’s greatest challenges.
“Flexible electronics will make possible new products that will help us address problems associated with food supply, clean water, clean energy, health, infrastructure, and safety and security,” Sitaraman said.
More than 20 researchers at Georgia Tech are involved in projects involving flexible electronics from the School of Mechanical Engineering, the School of Electrical and Computer Engineering, the School of Materials Science and Engineering, the H. Milton Stewart School of Industrial & Systems Engineering, and the Wallace H. Coulter Department of Biomedical Engineering at Georgia Tech and Emory University. Several interdisciplinary research intitutes at Georgia Tech are also involved in the projects, including the Institute for Electronics and Nanotechnology, Georgia Tech Manufacturing Institute, and the Institute for Materials.
“The area of flexible hybrid electronics has a unique appeal because of the inexpensive nature of printed electronics and the availability of a wide-range of substrate materials in large panel forms,” said Oliver Brand, a professor in the School of Electrical and Computer Engineering and the executive director of the Institute for Electronics and Nanotechnology.
Georgia Tech was one of the founding members of the Manufacturing Innovation Institute, which is headquartered in San Jose, Calif., and distributes research and development funds through competitively bid project calls. Industry-generated technology roadmaps drive project calls, timelines and investments.
In one of the projects, Boeing will partner with Georgia Tech researchers Tequila Harris, Suresh Sitaraman, Manos Tentzeris, and Rao Tummala to create a flexible array antenna that could be incorporated into a plane fuselage.
“By fabricating large and broadband antenna arrays using a combination of additively manufactured silver, carbon nanostructures such as graphene and nanotubes, and magnetic materials on several layers on flexible substrates, we will fundamentally stretch the flexible antenna technologies to frequencies better by one to two orders of magnitude compared to current state-of-the-art,” said Manos Tentzeris, Ken Byers Professor in Flexible Electronics with the School of Electrical and Computer Engineering. “This achievement will enable the first millimeter-wave flexible broadband wireless modules applications, such as real-world large-area Internet of Things, smart skins and wearable biomonitoring systems.”
In another project, Georgia Tech researchers Abhijit Chatterjee, Sam Graham, Suresh Sitaraman, Ben Wang, and Chuck Zhang will partner with Binghamton University and DuPont to perform a range of tests on flexible electronics to gauge how the mechanical and electrical characteristics will change under repeated bending, stretching, and twisting over a wide range of temperatures.
“Studying the electrical behavior of printed silver, copper, carbon, dielectric and other materials over multi-GHz frequency will provide unique insight that has not been addressed before,” Sitaraman said. “Similarly, repeated bending and stretching experiments and models under various thermal and humidity conditions will offer insight into cracking, debonding, and other failure characteristics of printed and assembled materials on a wide range of substrates.”
In the project headed by Hewlett Packard Enterprises in partnership with Georgia Tech, Stanford University, and the University of California – Santa Barbara, the team will develop process-design kits (PDK) for flexible electronics.
“PDKs are commonly used for complementary metal-oxide semiconductor devices for design and fabrication. However, when it comes to the nascent flexible electronics, design and fabrication tool kits are non-existent, and this project will accelerate developing and integrating such toolkits with commercial software packages,” said Madhavan Swaminathan, a professor in the School of Electrical and Computer Engineering, who is developing electrical models for the project using Machine Learning techniques.
In the fourth project, led by Binghamton University, Georgia Tech researchers Sam Graham, Olivier Pierron, Suresh Sitaraman, and Charles Ume will examine the reliability of wearable human health and performance monitoring devices through physics-of-failure models.
“Based on our experiments, we see that our protective barrier coatings on devices are able to provide protection, when the devices are exposed to phosphate buffered saline (PBS) solution similar to physiological fluids, and thus, Georgia Tech will make important contributions to wearable electronics,” said Sam Graham, a professor in the School of Mechanical Engineering.
The flexible electronics program will not only unleash a wide range of game-changing applications but will also dovetail with Georgia Tech’s mission to develop a highly-trained workforce, Sitaraman said.
“By incorporating the ideas into classroom education, capstone design courses, student internships, and external short courses, the program aims to develop a comprehensive workforce consisting of doctoral and master’s thesis students, practicing undergraduate engineers, product developers, and high-school students, and will position Georgia Tech as a leader in the development of a well-qualified and well-trained workforce to address different aspects of flexible electronics from research to practice to product development to manufacturing and economic growth,” he said.
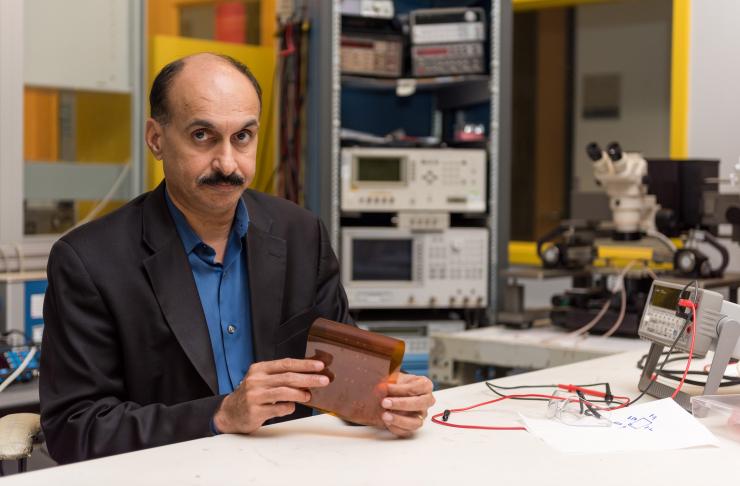
Suresh Sitaraman, a professor in the George W. Woodruff School of Mechanical Engineering who is leading Georgia Tech’s flexible electronics activities. (Credit: Rob Felt)
Research News